コロナ危機に克つ:日産自動車 先端技術を共有、社内リソース結集
日本インダストリアル・エンジニアリング協会(日本IE協会)副会長で、日産自動車常務執行役員パワートレイン生産技術開発本部本部長の村田和彦氏は生産性新聞のインタビューに応じ、100年に一度と言われる自動車業界の大変革に対応する中で、環境の変化に直面する従業員を支える取り組みについて紹介した。全固体電池やSOFC(固体酸化物型燃料電池)発電装置など革新的な技術を共有する社内技術展示会や、ベテラン従業員が悩み相談に応じる窓口を設置するなど、「やりがいと安心感」の両輪で意識改革を支援する。
やりがいと安心感で従業員支援
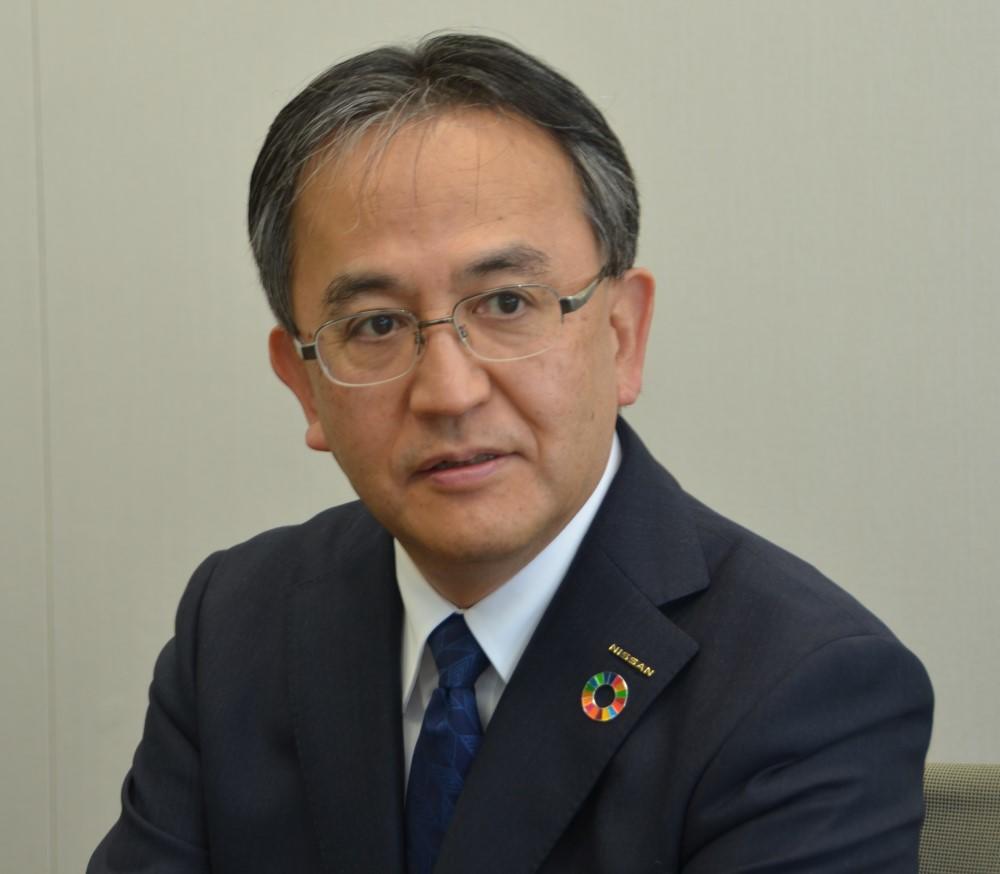
村田氏は「コロナ禍を経験したことで、社員は、『何が起こっても不思議ではない』という時代の変化にリアリティを感じるようになり、自動車業界を取り巻くさまざまな変化に対して正面から向き合うようになった」と話す。
そうした新しい技術への挑戦に対する、社員の「やりがい」を支援するために実施している取り組みの一つが、「社内技術展示会」だ。2028年度の実用化を目指して研究開発を行っている全固体電池や、多様な燃料と酸素との反応を利用して高効率に発電するSOFC発電装置など、世界をリードする最新のテクノロジーを社内で共有する。
村田氏は「新技術に関しては教科書を読んでも書いていない。それよりも現物を見て、担当者から直接話を聞くことで内容が分かり、『自分なら何ができるか』を考える効果が生まれる」という。最新技術を実感できればリスキリングも生きてくる。
社内には全固体電池の経験を持っていない人が多いが、プロジェクトは、バッテリー経験者だけで行うものではない。バッテリーの専門技術を持っている人が軸になるとしても、量産化までは社内のリソースの結集が必要になる。
村田氏は「電極材をスパッと切るとき、鍛造の型の技術を活用できる。また、材料を電子顕微鏡で調べて、介在物の有無を検査する技術も有効だ。このように現有技術の8割は、新技術のプロジェクトになんらかの形で生かせる」と話す。
コロナ禍を経験し、脱炭素への取り組みを「今やるべきこと」の最優先課題の一つとする認識が広まっている。会社も5年間で約2兆円を投資し、電動化を加速させることや、全固体電池を2028年度に市場に投入することを軸とした長期ビジョン「ニッサン アンビション2030」を打ち出したことで、従業員の意識改革を後押ししている。
一方で、新しい世界に飛び込んでいくことに不安を感じる従業員も少なくない。このような不安を和らげるために、キャリアデザインや人生設計について話し合う機会を設けたり、役職を終え、利害関係のないベテラン従業員が悩み相談を受け付ける窓口を設置したりしている。この窓口は、サントリーホールディングス傘下の企業が始めた「隣のおせっかいおじさん」(通称TOO)の活動を参考にした。
村田氏はこの活動について「昔と比べて希薄になった助け合うコミュニティの機能を、社内に再構築しようと始めた取り組みだ。やりがいと安心感の両輪を回して、新しい分野に果敢にチャレンジする組織にしていきたい」と語った。
(以下インタビュー詳細)
変化への強度高める必要あり 自動化やモジュール化推進
村田和彦 日産自動車常務執行役員 パワートレイン生産技術開発本部本部長インタビュー
新型コロナウイルスの感染拡大は、製造業にさまざまな教訓を残した。半導体などの部品・部材の不足により、生産に遅れが出ていることが代表的な影響であり、今後の対応策としては、対変動強度を持たなくてはならない。
コロナが製造業に残した教訓
環境の変化にフレキシブルに対応するための方法として、一つは自動化を進めることが大事だ。自動化率を高めることによって、需要が大きく変動した場合、人材を増やしたり、減らしたりせず、機械の稼働率の高低によって調整することが可能になる。
さらに、全生産工程の中で、モジュール化できる部分をつくっておけば、その部分だけを取り出して、需要が増えている工程の中に組み込むことも可能になり、変動に対する強度はさらに強くなる。
また、世界の動向を注視して、部品調達の状況を把握する必要がある。中国のゼロコロナ政策によって、上海がロックダウンになったことで、多くの生産工場が停止に追い込まれたことは記憶に新しい。適切な在庫を確保しておくことも教訓になった。
インテリジェント工場が始動
さまざまな環境の変化に対応し、クルマづくりのあり方を変えていく「ニッサン インテリジェント ファクトリー」を栃木工場に初めて導入した。このコンセプトによって、電動化技術やコネクテッド技術を数多く搭載した次世代のクルマへの対応や、匠の技を伝承したロボットによる最高品質の量産、人とロボットが共生する誰でも働きやすい職場、さらにはゼロエミッションの生産システム実現を目指し、脱炭素社会に向けた取り組みを加速させる。
日産は、これまで高品質で高効率な生産工程や高い技能を持つ匠の技術により、高精度なクルマづくりを実現してきた。しかし、コロナ禍の前から、自動車の生産を取り巻く事業環境は大きく変わりつつあり、それらの変化に対応していくことが大変重要だ。
従来の労働集約型の生産から脱却し、高齢化社会や深刻な人手不足に対応するための労働環境の改革に取り組まなければならない。また、気候変動やパンデミックなどの予期せぬ事態への対応も喫緊の課題だ。クルマの電動化や知能化、コネクテッド技術によって、クルマの機能や構造の高度化、複雑化が急速に進んでいる。
生産現場では、さまざまなチャレンジに取り組んでいる。車両のアンダーフロアに組み付けるエンジンやトランスミッション等のパワートレイン部品や、EV(Electric Vehicle:電動自動車)の大型バッテリーは、複数工程で専用リフターを用いて組み付けが行われていた。ICE(Internal Combustion Engine:内燃機関)、e-power、EVのようなパワートレインの仕様差の影響を受ける工程を、新開発のパレットシステムの採用により、一つの工程に集約、一括搭載する工程とした。
さらに、車体とアンダーフロア部品の寸法誤差を一台ごとに測定し、自動で位置合わせを行うロジックを開発することで、部品一括搭載の全自動化を実現した。このように、多様なパワートレイン、サスペンションユニットにフレキシブルに対応した次世代のアンダーフロア工程を実現することができた。
これからの製造業は、アセットやスペックの共有性を備えられるような、高い技術力を持っていないと、生産を継続し、生き残っていくことは難しいと思っている。
現在持っている設備を使って、これまで生産しているものだけではなく、これからの製品に対しても、使用可能とすることや、将来、技術が進化しても、モジュールを入れ替えることで、新しい製品の生産に対応できるようにすることが望ましい。
米国の金融政策がインフレの抑制のために利上げを進めたことで、円安・ドル高傾向が強まった。これによって、生産拠点を国内回帰させる動きが進むとの見方もあるが、円安を理由に生産地を変える戦略を取る企業は少ないと思う。
例えば、日産が新しいクルマを開発する場合、生産地を決めてから、実際に消費者に販売するまでには数年かかる。その時の為替のトレンドがどうなっているのかを予測することは難しいからだ。
日本のモノづくりを強くしたい
しかし、為替の動向を抜きにしても、日本のモノづくりを強くして、世界と勝負したいという気持ちはある。そのために、国内の生産技術力を高めるという考え方には賛成だ。
日本のモノづくりの確固たる強さを持って、日本からつくり、生産を開始し、海外へ展開するのが理想だ。
日本が付加価値で海外と勝負しようとする時、電動化は危機ではなく、チャンスになる。どの国もできていない新しい分野の技術にチャレンジすべきだ。ぜひ、そうしたいし、その力はあると思う。
量産化が難しく、付加価値の高い新技術は、絶対に日本でやるべきだ。もちろん、何年か経つと、こうした技術でさえコモディティ化するかもしれないが、少なくともそうなるまでには高い付加価値が維持されるはずなので、日本でつくるビッグチャンスだ。
実際、日産が開発競争をリードしている全固体電池は、技術的なハードルが極めて高く、当分は付加価値も高くなる。そうした付加価値の高い製品は、日本で生産し、技術の標準化を行なってから、海外で生産するという戦略だ。技術を自分たちの手の内にしておくことが重要である。
2028年の量産開始を目指す
2024年に横浜・新子安の工場内にパイロットプラントを立ち上げ、全固体電池の試作品の製造を開始する方針で、現在、その準備を急ピッチで進めている。日産のR&Dセンターでは、すでにプロトタイプのセルが開発されており、2028年から量産を開始する計画だ。
*2022年11月9日取材。所属・役職は取材当時。
お問い合わせ先
公益財団法人日本生産性本部 コンサルティング部
WEBからのお問い合わせ
電話またはFAXでのお問い合わせ
- TEL:03-3511-4060
- FAX:03-3511-4052
- ※営業時間 平日 9:30-17:30
(時間外のFAX、メール等でのご連絡は翌営業日のお取り扱いとなります)